Recommended Citation
Postprint version. Published in Metallurgical and Materials Transactions A, Volume 31, Issue 7, July 1, 2000, pages 1741-1752.
NOTE: At the time of publication, the author Trevor Harding was not yet affiliated with Cal Poly.
The definitive version is available at https://doi.org/10.1007/s11661-998-0329-1.
Abstract
The relationship between impact damage and the fatigue behavior of γ-TiAl has been examined. Axial fatigue specimens fabricated from cast Ti-47.9Al-2.0Cr-1.9Nb (to be referred to as 48-2-2) and Ti-47.3Al-2.2Nb-0.5Mn-0.4W-0.4Mo-0.23Si (to be referred to as WMS) alloys were damaged by impact under controlled conditions with a 60 deg wedge-shaped indenter to simulate assembly-related damage in low-pressure turbine blades. The level of damage produced was quantified and found to correlate well with the peak load of the impact event. The WMS alloy exhibited a greater resistance to impact damage due to its higher yield strength and lamellar microstructure. A measure of the ambient-temperature fatigue failure stress in the alloys was obtained by standard fatigue testing employing a step-loading approach. The failure stress of the WMS alloy was greater than that of the 48-2-2 alloy in the undamaged state. The relationship between impact damage and failure stress was examined using a threshold-based approach. These studies indicate that, for damage levels below a transitional flaw size, the failure stress is near that for undamaged specimens. At damage levels greater than the transitional flaw size, the failure stress can be adequately approximated using the threshold stress-intensity range (ΔKTH ) from long-crack growth testing. Fractographic studies were performed to investigate impact damage and crack-advance mechanisms, which match those observed in other alloys tested at room temperature.
Disciplines
Materials Science and Engineering
Publisher statement
Publisher website: http://www.springer.com.
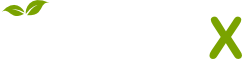
- Citations
- Citation Indexes: 10
- Patent Family Citations: 1
- Policy Citations: 1
- Usage
- Downloads: 636
- Abstract Views: 49
- Captures
- Readers: 6
Included in
URL: https://digitalcommons.calpoly.edu/mate_fac/45